Small Modifications
This page lists a few small modifications that I've made to the M250 in order to make it more usable. The modifications seemed too minor to be worth giving them their own page, so I've collated them here.
Drawbar
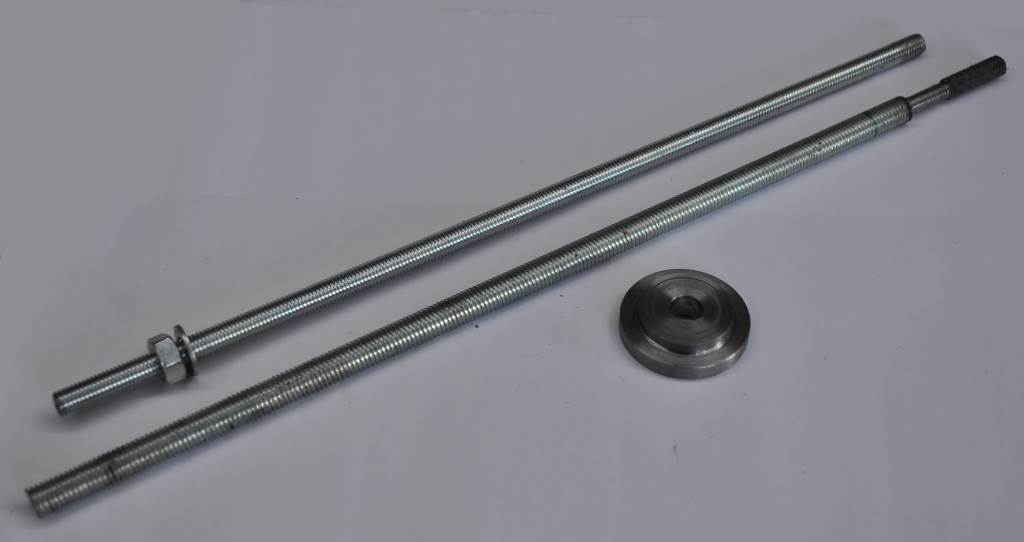
This photo shows a simple drawbar kit that I made for the M250. The washer in the bottom-right of the picture is 50 mm outer diameter and 12 mm thick. It has a 12 mm bore and is reduced in outer diameter to 35.5 mm for a thickness of 5 mm. This goes into the rear of the spindle and holds the threaded bar central on the bore for use as a drawbar.
The bar at the top of the photo is simply a piece of M12 threaded rod with a nut and washer on it. This is used for MT3 tooling that has an M12 drawbar thread and couldn't be much simpler! The other bar is also a piece of M12 threaded rod, so can use the same nut and washer and has the same fit in the washer. The right-hand end has been turned down and threaded 3/8" BSW, which is used as the drawbar thread for some MT3 tooling. Using M12 threaded rod for most of the length means I don't have to try to find an imperial nut and spanner in order to use this drawbar.
Swarf Shield
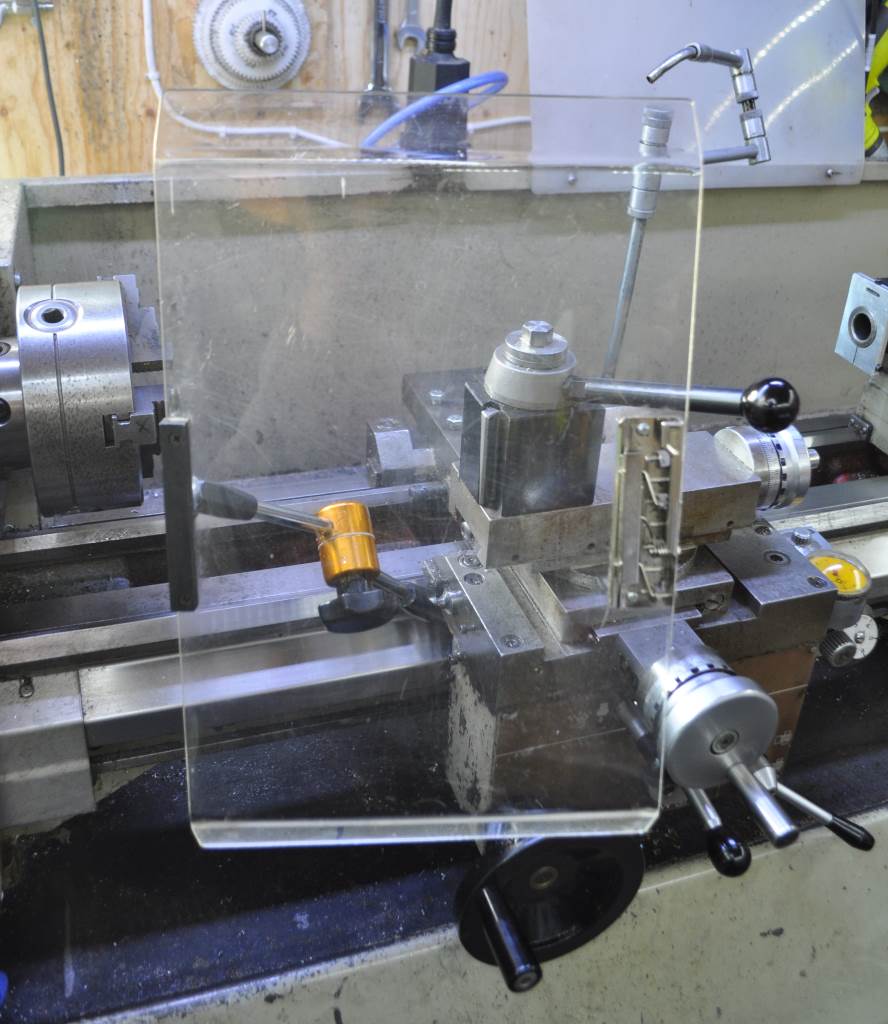
I may have mentioned on several other pages on this website how much I hate clearing up swarf from every nook and cranny of the garage. The carriage on the M250 has an M8 threaded hole on the left-hand side, originally intended for use with a carriage stop I think. A few years ago, I bought a safety shield with a magnet stand from arceurotrade. The flexible arm attaches to the magnetic base with an M8 screw, so I attached this to the lathe carriage and it gives me a handy shield to stop swarf flying all over me when I'm machining free-cutting materials.

This photo shows the way the arm is mounted in a bit more detail; hopefully it's self-explanatory. It can be swung out of the way very easily or removed completely if necessary (although I haven't found it necessary since fitting the shield).
Change Gears
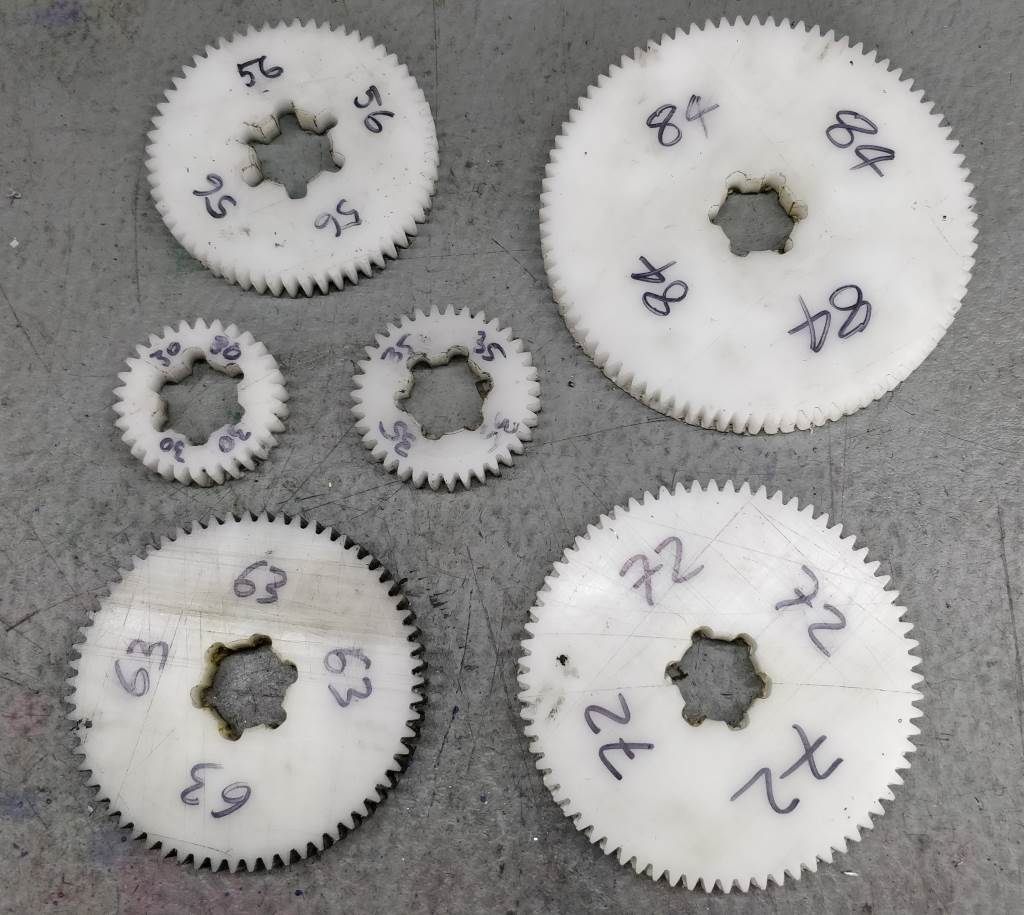
My Harrison M250 came with five change gears: 22 teeth, 40 teeth, 44 teeth, 80 teeth and 88 teeth. In combination with the gearbox, these allow virtually any metric thread to be cut (and in practice, any thread I'm likely to cut can be done with the standard "G" configuration of 44:88, 40:80 so the 22 tooth gear rarely gets used).
However, there are times (such as when making the 3/8" BSW drawbar mentioned above), that I need to cut imperial threads. Change gears for the M250 are expensive and rarely available. Considering how infrequently I would want to cut an imperial thread, I really didn't want to spend much money on them. Therefore, I decided to make my own. I bought a sheet of 10 mm thick acetal and laid out a simple template for the most useful (module 1.5) gears. This template was printed out and stuck onto the acetal sheet. My father's vertical bandsaw was used to roughly cut out the gears.
The M250's change gears have a spline on the inner bore. Investigation showed that the inner diameter was critical, as was the width of the spline teeth, but the outer diameter of the bore was not important. This simplified manufacture significantly. Each roughly cut gear was mounted on the faceplate on the M250 and the inner diameter bored carefully. It was then mounted on a mandrel using the inner diameter and skimmed to size. The same mandrel was then used on my combination rotary table / dividing head along with some gear cutters made using the technique described by Mike Cox. Finally, the gears were mounted on the rotary table and a 3 mm end mill used to cut the spline teeth. The eagle-eyed among you will notice that I miscalculated slightly on the 56 tooth gear and cut the teeth a bit deep. As the outer diameter isn't used in the spline engagement, this doesn't matter at all, but I corrected it for the other gears anyway.
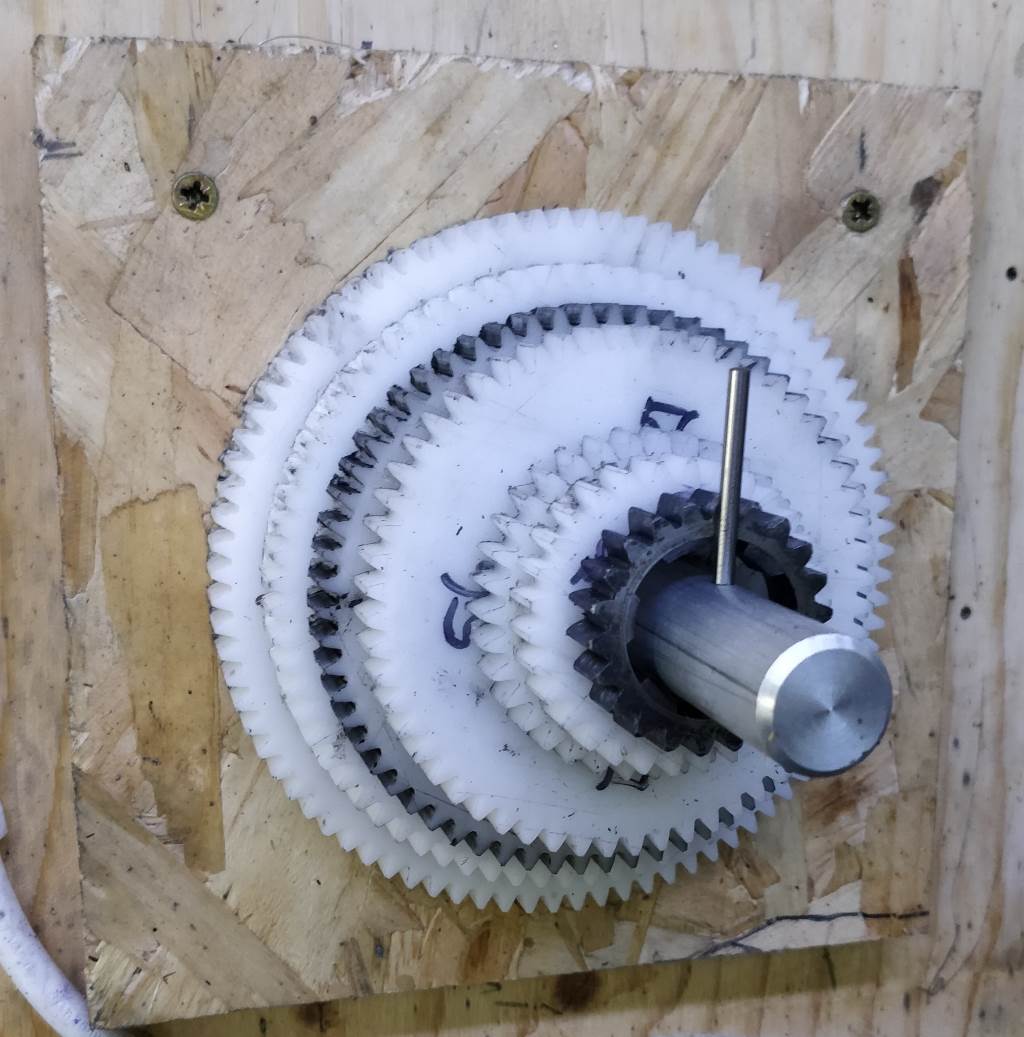
This photo shows how the gears are stored on the wall; hopefully this is self-explanatory.
In addition to the metric threads I could make with the standard gears, the gears that I have made allow me to make most mod threads (for worm gears) and most common imperial threads. There are a few imperial threads that aren't available but I would imagine they're unlikely to be needed (and I can always make some more gears if they're required). I've created a change gear calculator that can be used to figure out which gears to use for any particular threads that are needed. There's also a simple calculator for working out whether a thread dial indicator can be used.
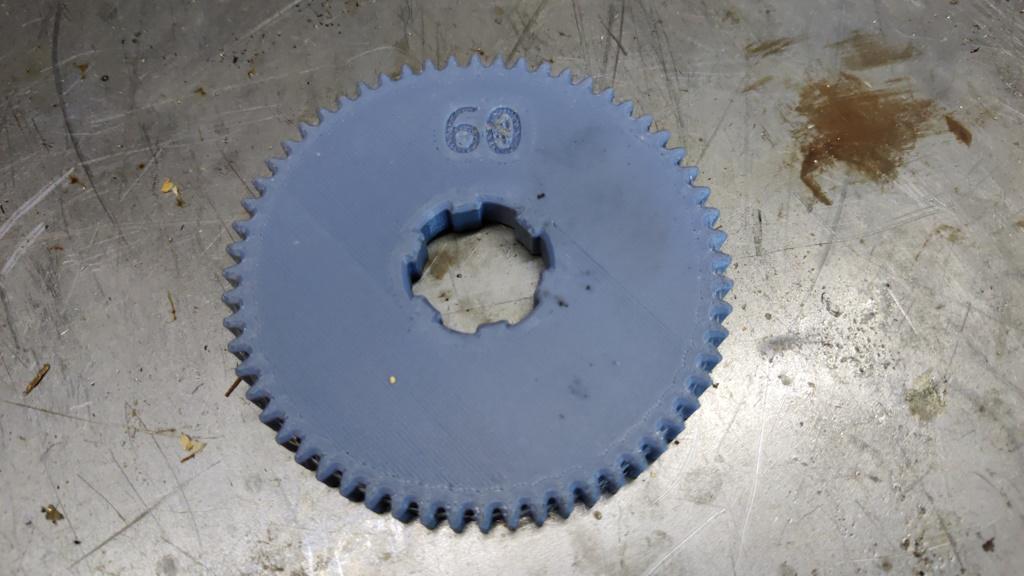
This photo shows a gear I made after getting a 3D printer. I needed one more gear in order to cut an obscure imperial thread and I thought it would be interesting to see whether a 3D-printed gear would work. I printed it with 5 perimeters (rather than the 2 that I usually use), but otherwise the normal settings I would use for any other 3D print. It worked perfectly and I've since used it for a few other parts. With the free on-line CAD tool OnShape, it was extremely simple to model the gear and it would be very straightforward to make more gears. You can see the CAD model here.
This website is free and ad-free, but costs me money to run. If you'd like to support this site, please consider making a small donation or sending me a message to let me know what you liked or found useful.